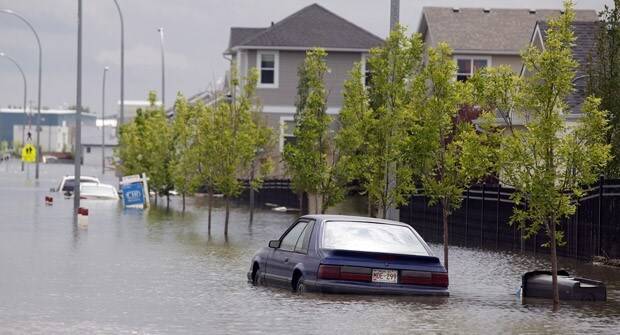
The ServiceMaster by Rice team out of Des Moines was asked to join a Disaster Restoration team to help with water and mold remediation after a large flood in June of 2013.
The High River in Canada flooded its banks and filled residential homes and commercial buildings in High River, a town of 12,000 people with 5,473 homes. The water damage caused by this event was so extensive that it required the complete evacuation of this town before the Disaster Restoration could even begin. Much like areas of Iowa and the cities of Des Moines, Clive and West Des Moines during the floods of 1992, this community was not prepared for a disaster that was referred to as a “500 year flood.” The rising water damaged the water treatment facility, the electric power substations in the area and the road infrastructure. Most residents had to leave their homes and belongings behind with little warning and no idea of when it would be safe to return.
With our expertise and efficiency in Disaster Restoration and mold remediation, the ServiceMaster by Rice joined the disaster relief efforts in a six week mold and water remediation project. Most of the residential homes sustained water damage from the river overflowing, resulting in flood damaged residential homes with average of six to eight inches of water. After the water receded and most of the water was extracted, the ensuing project changed in scope from Disaster Restoration efforts to water and mold cleanup.
ServiceMaster by Rice Crew Starts Disaster Relief Process
Our crews started the process by loading equipment in our Des Moines warehouse for the water and mold recovery effort. Trucks, vans and trailers were loaded with low grain dehumidifiers, air movers, air scrubbers and generators to handle any type of water mitigation and mold remediation project we could have encountered. Our certified mold remediation technicians prepared supply lists and manifests for crossing the border while our water mitigation repair technicians oversaw the loading and inventory of all the tools and supplies needed for the extensive water damage. All vehicles making the trip had to have signs saying Disaster Recovery Emergency Service and passports for all Disaster Restoration personnel were required.
The 1,500 mile trip to the town of High River included project management, water mitigation and mold remediation personnel, along with thousands of pieces of equipment, tools and cleaning supplies and personal protection gear. Chemicals were not allowed to cross the border so any chemicals needed for sanitizing, mold clean up and the water mitigation process had to be purchased north of the border. Any personnel working on this project had to commit to a 6-week minimum trip away from their family and friends. The commitment the team showed while working on projects like this was truly amazing.
Water Mitigation Services Disaster Recovery
Disaster Restoration Team Arrives
After ten days on the road, our disaster team finally arrived at their destination. The delay was caused because of the complexity of the project and the intricate border crossing.
Upon arrival at the camp they were introduced to the facility manager and they attended an orientation meeting. A company called Clean Harbor had setup the man camp where all personnel stayed during the project. This man camp was very impressive, with each employee having their own room with TV, bed and bathroom. The camp supplied all the food they could want any time of day.
ServiceMaster Team Scopes out Water and Mold Damage
When the flooding finally started to recede back to the banks of the river, five long weeks later, the damage was extensive and had devastated hundreds of homes. Five hundred of the homes damaged were declared uninhabitable for humans. The intense mold and water damage and the amount of devastation left behind required a detailed Disaster Restoration plan that included mold remediation and a water mitigation plan for any structural wood that could be salvaged.
Disaster Recovery Effort Begins with Mold Cleanup Process
Eight weeks after the flood water entered the town, crews from both Canada and the United States were in place and ready to start the water mitigation and mold remediation projects on each home damaged by the floods. Working with health officials, each project began with employees wearing full protection gear. The mold types were unknown and the amount of mold within each structure was extremely high and dangerous. The health issues that can be associated with black mold or (Stachybotrys) along with E.coli, made safety the top priority. Removing all the homeowners’ belongings was the first item to address. The belongings that were damaged had to be inventoried and discarded. Any contents that were not damaged were cleaned and placed in storage containers for the homeowner to look through later on.
After the homeowners belonging had been addressed, structural engineers and health officers reviewed the building for any safety concerns. If the structure was deemed safe to start the water and mold mitigation, a work order and scope of each loss was provided after a Disaster Restoration or water mitigation crew assessed the home. Because of the high level of mold in the homes and the unstable ground left by the water damage, the project manager’s job responsibility was first and foremost the safety of the crew.
The process started by removing most of the mud left behind by the flood waters. Part of the difficulty was that each home had no power or water; generators were set up to operate the air scrubbers to minimize the airborne levels of mold that would be disturbed during the removal of the affected building structure. The process of removing the bulk of contaminated materials in order to start mold clean up, including the removal of drywall, insulation, carpeting and padding and disconnecting of heating and cooling systems, it ended up being a two to three day process on each home.
Using our Expertise in Water Mitigation and Mold Remediation
After all non-salvageable building systems and materials had been removed, the process of cleaning and sanitizing the remaining salvageable building materials started. First off, all affected areas had to be power washed and the water added to an already wet home had to go through a water extraction process with our truck mount units. Each area of the home was power washed and the water was extracted to the outside environment to capture and remove the bulk of the growing mold spores. This cleaning process would normally take one to two days, then the drying process would start with a second cleaning process after drying an area of the home.
With no electricity, heat or water, all equipment needed for the mold clean up and water mitigation required a portable power source to run the low grain dehumidifiers and air movers along with air scrubbers and temporary heating units. During the drying process each residential home was checked daily. Most homes required five to eight low grain dehumidifiers, 25 to 35 air movers and one to two air scrubbers along with all the power cables and spider boxes used to distribute the power required to operate all the mold and water mitigation equipment. When an area of the home was completely dry this area would receive a detailed cleaning that consisted of wire brushing areas that had been discolored from the mold damage. A detailed Hepa vacuuming of all surfaces in the dry area would be performed and this area would then be isolated if possible. The drying process would take anywhere from 6 to 14 days depending on the building materials that were left.
After the structure was deemed completely dry, testing would consist of a visual walk through of the entire building, searching for any and all potential health hazards associated with mold damage. Air quality samples testing for mold types were taken in each area of the home and lift testing would be done on any hard-to-reach reach area of the home to insure mold levels were below the known safety standards. All mold samples were analyzed by the health department and mold testing results were communicated to the project manager. Any mold testing results that did not pass to their standard resulted in a complete mold clean up of the entire property until the structure passed the clearance testing. Once the structure was passed, the homeowner was given access to their property for the remodel process.
ServiceMaster Successfully Helps with Disaster Relief and Mold Cleanup
The ServiceMaster Disaster Restoration team completed 263 homes over a 12 week period after the flood waters receded. All homes passed mold clearance testing and all homeowners are planning on moving back in as soon as the heating, cooling and electric systems are back online. This entire project was deemed a success and our SRM group signed a seven year contract to assist our Canadian friends in any large scale disasters that may need our expertise in the future. No employees were hurt during this project and credit must be placed on the great project management team on site. If our team can handle a six week long, large scale mold remediation and water mitigation project, imagine what we can do in your home.